概要
P点(Potential failure) と F点(Functional failure)
P-Fカーブ(P-F曲線、P-F curve)は、機械や装置が何らかの劣化や変化を起こし、それが検知・認識できるポイント(P点)から、設備やシステムに実害や障害が発生し機能が喪失されるポイント(F点)に至るまでを、横軸に時間、縦軸に機械の状態、或いは故障への抵抗力(Resistance to failure)を取る曲線です。
この2つの点(Functional failure, Potential failure)の頭文字から、P-Fカーブと呼ばれ、概念的な表現であるため、単位を持たない無次元の曲線図です。
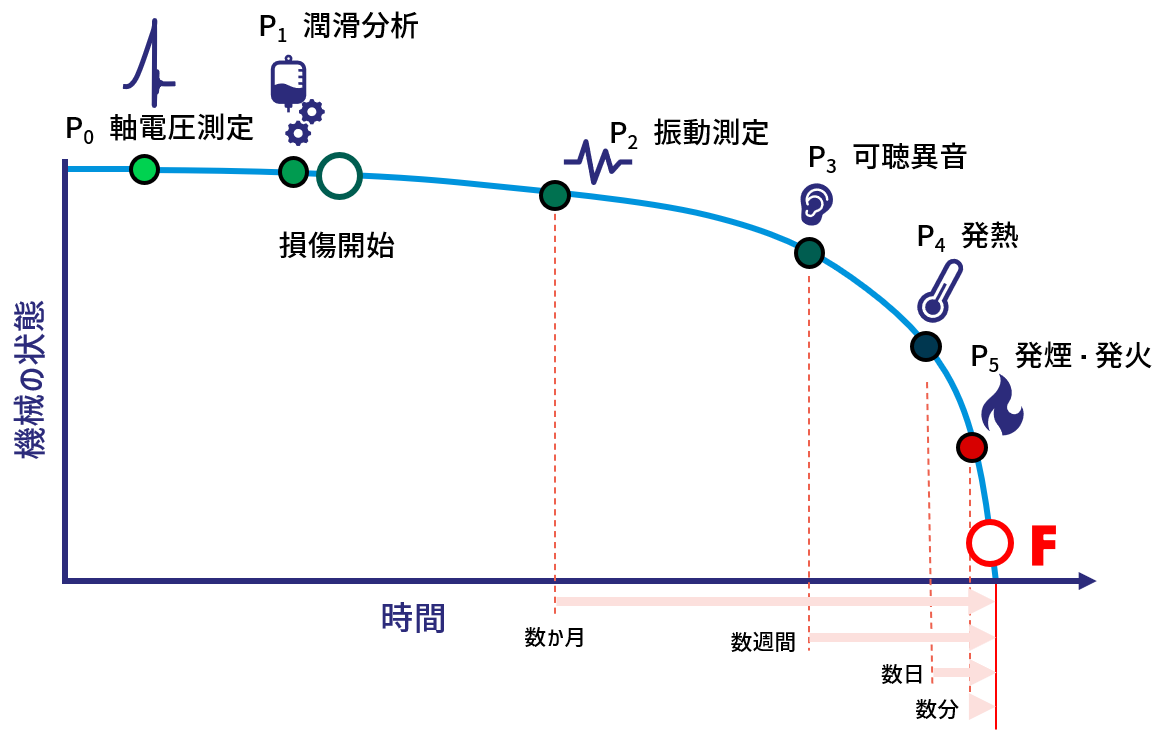
図1 P-Fカーブ(P-F曲線)の例
P点からF点までの間隔をP-Fインターバルと呼び、機械や設備それぞれの重要性やダウンタイム損失のスケール、復旧までに必要な時間(MTTR)や修繕復旧費用などを総合的に検討して、TBM(時間基準保全=Time-based Maintenance)や、CBM(状態基準保全=Condition-based Maintenance)など、手段を変えて保全活動を行います。
保全予防(Maintenance prevention)など、不具合を発生させる要因そのものの排除などを目的として、上述のP点・F点に加え、機械設計時(Design)と機械据付時(Installation)を加えた、D-I-P-Fカーブと呼ばれる曲線が提唱・利用されている場合もあります。
状態監視(コンディションモニタリング)
不具合が発生する頻度をより低くしながら、P-Fインターバルをより長く、つまり異常がより早期に検出できるよう保全することが機械や設備にとっては望ましく、故障の根本原因となる要因の特定や監視を行いながら、それ自体を取り除くことが、設備運用の最適化にとって非常に重要です。
ここからは、コンディションモニタリング(Condition monitoring)の技術の一部をご紹介します。
軸電圧測定(Shaft voltage testing)
回転機、特にインバータ駆動の電動機(モータ)やそれに連結する機械(減速機・圧縮機・ポンプ・送風機など)では、軸受で電位差(電圧)が発生している場合があります。それを検知するための手段が軸電圧波形測定です。
軸電圧波形の振幅は、軸受の油膜厚さに大きく影響を受け、同時に軸電圧波形の振幅に影響を与えます。ストライベック曲線と油膜厚さで示される通り、回転機の回転速度、潤滑粘度、荷重と潤滑の質に影響を受けます。
油膜厚さが大きくなればインピーダンス(Ω)が大きくなり、オームの法則で軸電圧も大きくなる傾向にあります。そのため、一般的なテスターを使って、軸電圧を実効値Vrmsで測定することもありますが、後述の軸電圧テスター(オシロスコープ)を用いて測定されます。また潤滑が劣化してくると金属接触が増えたり、潤滑のインピーダンスが低下することでも軸電圧の振幅は小さくなるため、状態が最も良いときに測定することで、軸受や潤滑を劣化させる潜在的な軸電圧を測定することができ、プロアクティブ・メンテナンスとして、問題の対策効果測定にも活用することができます。また、軸受インピーダンスが高い状態である新しい潤滑や新しい軸受においては、EDM放電時のdV/dtにおけるdtが数ナノ秒であることがありますが、上述の通り潤滑が劣化しインピーダンスが低下すると、この時間tも長くなる傾向にあります。
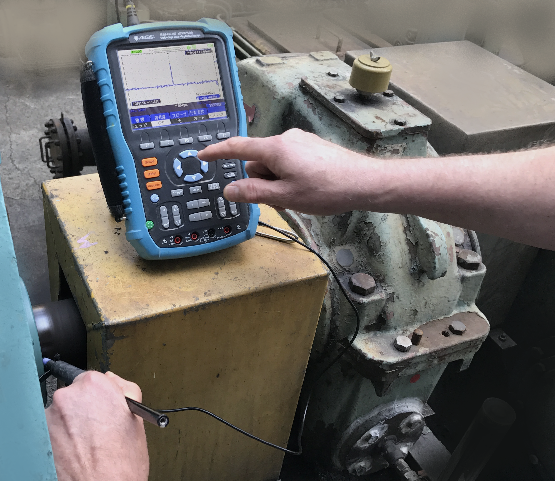
イージス軸電圧テスター
イージス軸電圧テスターは、米国Electro Static Technology社が開発し販売している、2チャンネルの100MHzデジタルオシロスコープです。回転体の軸と機械筐体間、つまり軸受内輪電位と軸受外輪電位との電位差を測定することに特化した設計で、簡単に軸電圧波形を測定することができます。軸受に何らかの損傷を生ずる前から軸受放電が確認できるため、非常に早い段階で活用できる分析方法です。その一方、軸受における電位差(電圧)を測定しているため、軸受インピーダンスが下がってくると軸電圧波形の振幅値も下がります。つまり、潤滑寿命で油膜が形成されにくくなった状態や、潤滑中の鉄粉濃度が上昇すると、潤滑自体のインピーダンスが下がり、軸電圧の振幅も下がります。そのため、F点に近づくと、波形として確認しづらくなる傾向もあります。潤滑分析(Lubricant analysis)
潤滑の分析手法は、潤滑の種類や分析する目的などで、潤滑油成分分析、鉄粉濃度計、ミリポアフィルター、自動粒子計測器、フェログラフィ法、SOAP法など多くの手段があります。切粉や錆、繊維屑など、機械が作られる際に生じた汚染物質であるか、或いは、水や塵埃、バクテリア、赤外線などで汚染・劣化した機械稼働後に生じた汚染物であるかなど、対象汚染物によっても、分析手段や分析方針が変わります。
超音波測定(Ultrasonic analysis)
超音波測定は、人間の可聴域周波数(20Hz~20kHz)よりも高い周波数を測定する方法で、故障の根本原因を特定することに優れています。特に壁などを通過せず反射し、直進する(指向性)特徴があるため、空気がガス漏れの場所特定などができたり、転がり軸受の早期の異変も検出できる場合があります。
同じ超音波帯域を用いる測定手法に、AE(アコースティック・エミッション=Acoustic Emission)法とSPM(ショック・パルス・メソッド=Shock Pulse Method)法などがあります。
SPM法は2つの金属が接触するときに発するショックパルス(圧力波)が、32kHz前後という特徴を活かし、スウェーデンで考案された技術で、周波数が高く減衰の早い圧力波を使って、軸受などの状態を分析する手法です。軸受情報と回転数から損傷や潤滑の状態が分析できます。
AE法はAcoustic Emission、すなわち音響の放射を検知する手法です。物体が変形・破壊するときの歪みエネルギーが伝播するものや、すべり運動の時に発生する弾性波(Elastic waves)を検出します。AEの周波数帯域は1kHz~1MHzなので、一部可聴域(20Hz~20kHz)ともオーバーラップしますが、設備診断で使用される場合、数10kHzから100kHz以上の周波数帯域が対象となります。転がり軸受の分析手法として、振動測定では一般的に回転数に影響を及ぼされる一方で、AE法は回転数の影響を大きく受けない特徴があるため、押出し機、アジテータ、圧延機など、加速度が小さい低速回転で振動診断が向かないため、低速回転の異常検出では、AE法が適している場合があります。
振動測定(Vibration analysis)
最も多く活用されている状態監視の手法の1つと言えます。市場で普及している振動測定器は、計測対象の機械に固定し常時監視するタイプと、保全スタッフが定期的に計測器をもって巡回するハンディタイプとに分けることができます。
計測する対象により発生する周波数も異なるため、周波数の違いによって、変位(Displacement、単位:µm, mm)、速度(Velocity、単位:mm/s, cm/s)、加速度(Acceleration、単位:m/s2, g)を使い分けて計測・分析されます。
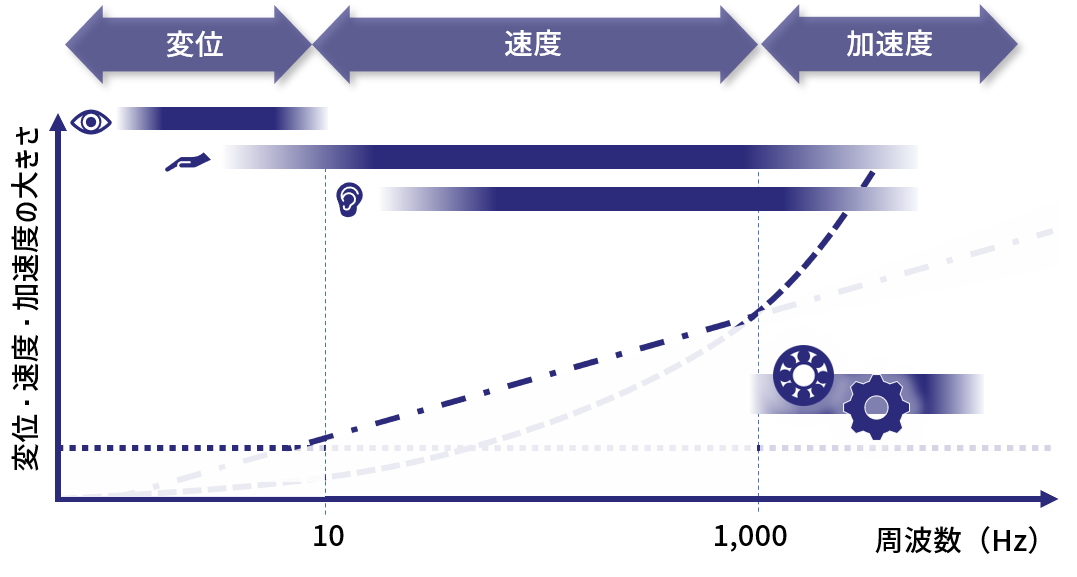
図2 転がり軸受・歯車の振動周波数
振動測定モード | 変位 [DISP] |
速度 [VEL] |
加速度 [ACC] |
---|---|---|---|
周波数帯域 | ~10Hz | 10Hz~1kHz | 1kHz~ |
検知対象例 | 地震など | アンバランス ミスアライメント 緩み 電磁振動など |
転がり軸受の異常 歯車異常など |
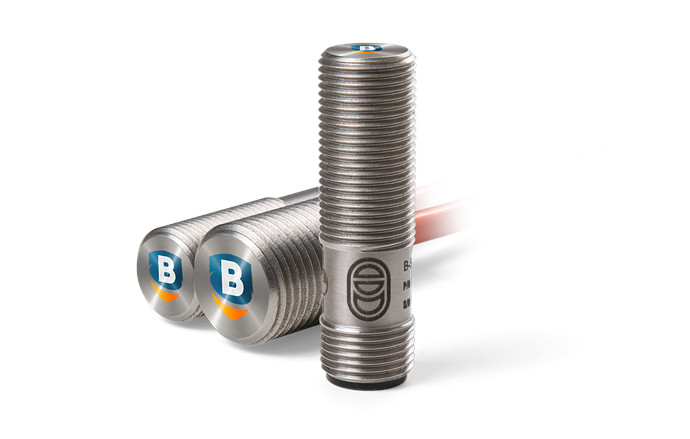
B-Safe スピンドルモニタリングシステム
Balance Systems社のB-Safeは、振動および温度の状態分析によってスピンドルをはじめとした工作機械の診断をするために最適化されています。小型化されたセンサーを測定箇所に直接取り付けることで、様々な異常をリアルタイムで監視できます。最新バージョン「X」では予知保全機能の充実化が図られ、マシンのダウンタイム削減に更なる力を発揮します。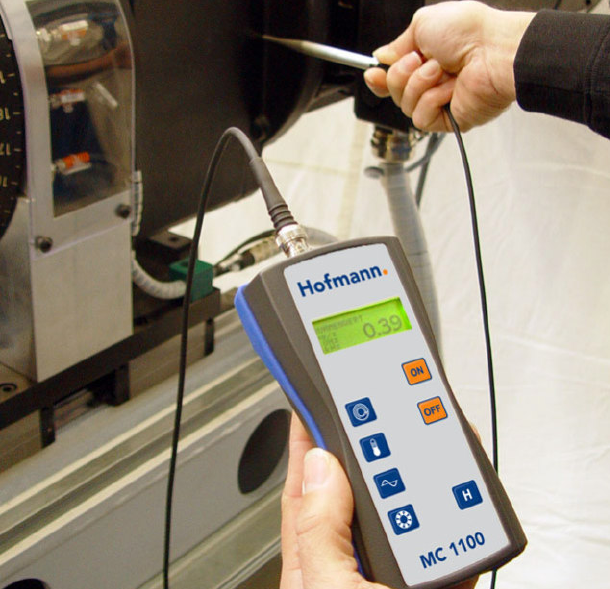
Hofmann 振動測定システム MC1100
Hofmann(ホフマン)社のMC1100は、1台で機械の振動値測定や転がり軸受の状態監視、回転速度の計測などを測定することができます。また、オプションで温度測定やベルトテンションの計測もできます。シンプル&クイック操作をコンセプトに、ISO 10816-1-6に準拠した振動測定器で、バッテリーを内蔵しており、2時間の充電で6時間の測定が可能です。MC1100は3種のバンドを持っており、低速から高速までカバーします。ボールベアリングのスペクトラム振動測定は衝撃モーメント法のgSP値で表わされ、ボールベアリングの状態変化を的確に捉えます。
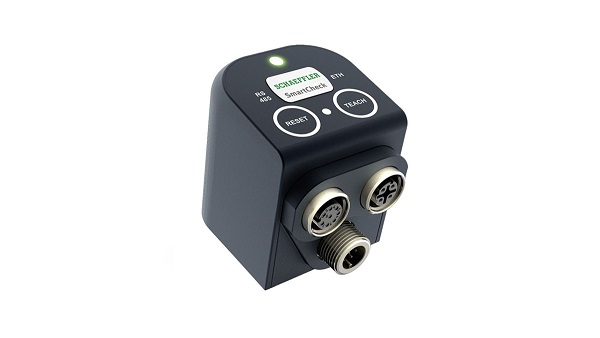
シェフラー SmartCheck
SmartCheckは、世界トップクラスの転がり軸受メーカ・シェフラー社が開発した常設型の振動測定装置で、転がり軸受の損傷、アンバランス、ミスアライメントを早期に検知し、予知保全を最適化し、設備機械の安全性・収益性・信頼性・安心感を改善し保全間隔の延長します。
アプリケーションは、モータおよびギアモータ、真空ポンプ・流体ポンプ、ベンチレータおよびファン、ギアボックスおよびコンプレッサ、スピンドルなど、様々な機械の予知保全を最適化します。
可聴音分析(Audible noise analysis)
人間が聴くことのできる周波数帯(20Hz~20kHz)は、異常検知の最も歴史の長い状態測定方法の1つで、お医者さんが行う聴診器による診察と似ています。
転がり軸受を使用した機械では、聴診棒を使うことでその軸受の音を聞くことができます。
初期投資が小さい一方、聴診する人の技量や測定場所、周辺環境などにより判定が変わる可能性もあり、また機械数が多い場合は、それぞれの観察結果を残すことも含め、とても大きな労力や時間が必要となる場合があります。
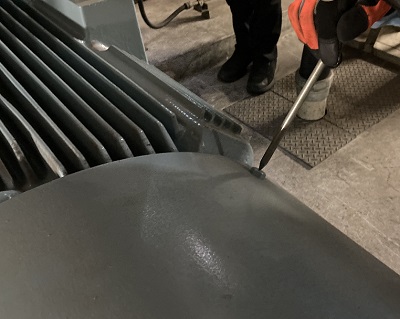
温度測定・サーモグラフィ(Thermography analysis)
機械の劣化や摩耗が進んだり、電気的な異常が発生すると、当該箇所の温度が上昇します。機械的な軸のミスアライメントやギアボックスの異常など、サーモグラフィを使用することで異常の可視化ができるため、近年注目が高まっています。ただ、温度上昇している状況は既に、機械や装置として、致命的な状態に陥っている場合が多いため、他の手段とともに活用することが重要です。
サーモグラフィ以外にも、熱電対や非接触温度計など、用途や目的に合わせ測定を行うことで温度上昇を察知できるようになります。